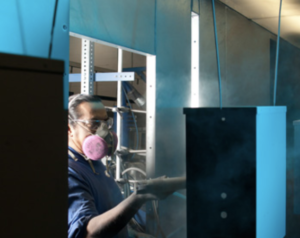
While many contract sheet metal fabricators and machine shops offer powder coat finishing services, the vast majority outsource or subcontract out the work to third parties. However, there are substantial benefits to working with a fab shop that provides integrated manufacturing services, including in-house powder coating, all under one roof.
5 Benefits of Using a Contract Metal Fabricator and Machine Shop with In-House Powder Coating
There are five main benefits of working with a metal fab and machine shop with end-to-end manufacturing capabilities like in-house powder coating:
- cost savings
- quality control
- reduction of waste & rework
- speed & efficiency
- customer service & satisfaction
Cost Savings
When powder coating services are kept in-house, it means that contract metal fabricators are able to accurately quote costs for a project down to the dollar, and without any additional mark-ups included by using outsourced suppliers or vendors. This results in savings for their customers, who don’t have to pay more, over and beyond what the service actually costs to complete. There are also no unfortunate surprises regarding the project’s costs, because in-house powder coating gives fab shops complete control over the process, allowing them to fully understand from the start what the project will entail and quote it with confidence.
Quality Control
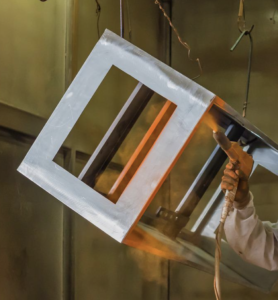
When powder coating is outsourced to a third party, it can be difficult to control quality, especially when it comes to metal finishing projects. For instance, it’s not uncommon for a metal part’s surface imperfections to lack complete and even paint coverage when powder coating is completed offsite. This is especially true with gloss finishes, which make it much more difficult to hide scratches and other marks than when matte finishes are used. In-house powder coating specialists have the experience and training to identify these issues or flaws in the metal parts prior to painting and work alongside the quality control team to address them before they move on to be finished.
Beyond surface imperfections, in-house powder coating can be closely supervised by a team that understands how the part should ultimately look and perform, meaning problems with the paint itself, like color mismatches and non-uniform thicknesses, can be more quickly addressed and most often completely prevented in the first place.
Reduction of Waste & Rework
Painters who work in environments that only handle one process are less likely to have this level of metal fabrication-specific knowledge than those who work within a metal fab facility, which means that defects may not be caught until after they are painted and sent back to the fabricator for completion of other processes like assembly and integration or shipping and delivery. When this happens, it can negatively affect lead time and add to the cost of fabrication due to wasted parts and rework.
Additionally, shipping metal parts back and forth can lead to other types of damage, both when shipping to and from an offsite powder coating service. Shipping to the vendor can cause pieces to rub against each other creating scratches or other marks on the metal surfaces that may not be addressed adequately during the powder coating process. Shipping from the vendor back to the fabricator can have similar issues, only now, the result is damage to newly-applied paint — yet another cause of part waste and rework.
Speed & Efficiency
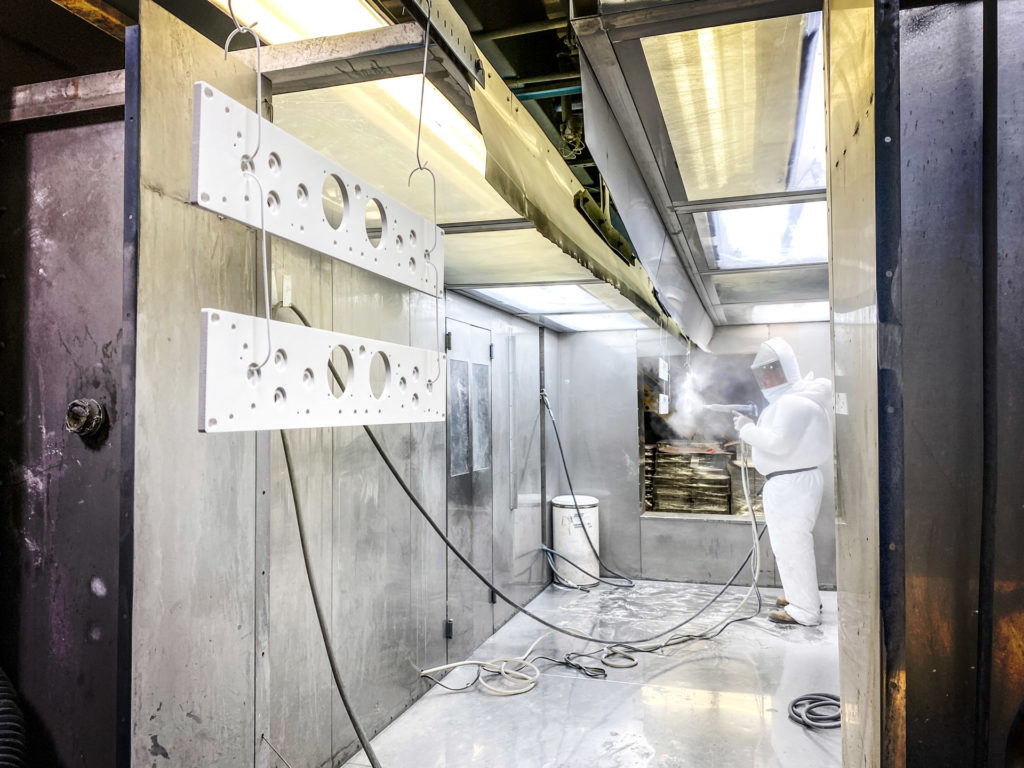
Sending products to be finished by an offsite powder coating company lengthens lead times and ultimately slows down the product’s speed to market, sometimes by weeks. Depending on the order size, in-house powder coating can be turned around in as little as a day when it’s part of an end-to-end fabricated metal and machining project.
Outsourcing powder coating also creates fluctuations in lead-time estimates that are rarely an issue when all manufacturing services are provided in the same place. Once a part leaves the fabricator’s facility, they relinquish most of their control over when they might get that part back and on its way to being completed and delivered to their customer. In order to avoid disappointing their customers and losing business, it’s standard to build substantial “wiggle room” into delivery estimates when an outsourced powder coating service is used. In-house powder coating does not require that type of padding to be built into estimates, leading to faster delivery of finished products.
Customer Service & Satisfaction
When powder coating services are kept in-house, it means the fabrication team who is managing the project is able to provide better and more thorough service to their customers as they are able to keep an eye on the project from start to finish. And because fully-integrated metal fab shops are able to deliver higher-quality manufacturing outcomes faster and at lower costs, it’s easy to see in-house powder coating might be considered a significant value to their customers, too. For fabricators who emphasize customer satisfaction, the investment in value-added manufacturing processes like powder coat lines is well worth the price.
Why don’t most contract sheet metal fabricators offer in-house powder coating?
Most metal fab shops don’t offer in-house powder coating for two reasons.
In-House Powder Coating Lines Take Up Valuable Floor Space
Setting up an in-house powder coating line, especially one that is automated, requires adequate space. Small and even mid-sized fabricators generally don’t have space on the shop floor to add an in-house line to their facility, especially if they only have one location. When space is at a premium, there are likely other capabilities they need to offer that will offer a greater overall return. As it’s not unusual to outsource powder coating services, the lack of in-house capabilities is unlikely to be a non-starter for their customers, especially if they are unaware of the benefits of integrated manufacturing operations.
In-House Powder Coating Lines Are Expensive
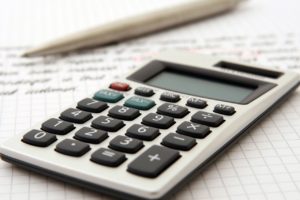
Automated in-house powder coating lines are costly. Purchasing and installing a new line for a single facility can cost upwards of $750,000. It’s a big investment, and not one that many metal fabricators are able or willing to make, especially when outsourcing powder coating processes is considered an acceptable practice.
Essentially, the handful of contract fabricators with in-house powder coating capabilities, like EVS Metal (who has four automated lines), have not made the investment because it’s cheap or easy, but instead, because they value the control it gives them over the entire manufacturing process, from engineering to delivery. This gives these companies a substantial competitive advantage in terms of the value they are able to provide to their customers in terms of cost, efficiency, quality, speed and customer service.
Looking for a commercial metal fabricator with in-house powder coating capabilities for your next project? EVS Metal has automated lines at each of our four American facilities located in New Jersey, Pennsylvania, New Hampshire and Texas. Ready to learn more? Request a quote online, or give us a call at 1-888-9EVSMET.